With the cost of living crisis wreaking havoc on UK household budgets, we could be facing a Dickensian style Christmas this year.
This time last year was strong as consumers were keen to embrace a festive period free of lockdowns and Covid-related restrictions but we’re hearing that 60% of Britons intend to cut their spending this Christmas. The Bank of England has recently raised interest rates and issued the grim warning of a long-lasting recession so what’s going to become of this year’s “golden quarter” and what does it mean for warehousing?
So far, all evidence is suggesting that the next few months are going to be deeply unpredictable. When looking at the warehouse space required, businesses are trying to work out what to expect. Will people spend more on home entertainment and less on going out, or vice versa? Will families focus on their children and forego presents for adults, or will Christmas indulgences still make it into online shopping baskets as consumers tire of financial doom and gloom and splurge on much needed enjoyment? Will shoppers be searching for even more Black Friday bargains as they feel the squeeze of rising energy bills, or will they be forced to budget carefully and put off Christmas spending until the last minute? Will the World Cup have an effect? We know that the Women’s Euro 2022 tournament was predicted to bring £54 million of extra economic activity to the UK and that the triumphant success of the English women may actually have doubled that impact so should retailers prepare for a boom and look for additional warehouse space in order to cope?
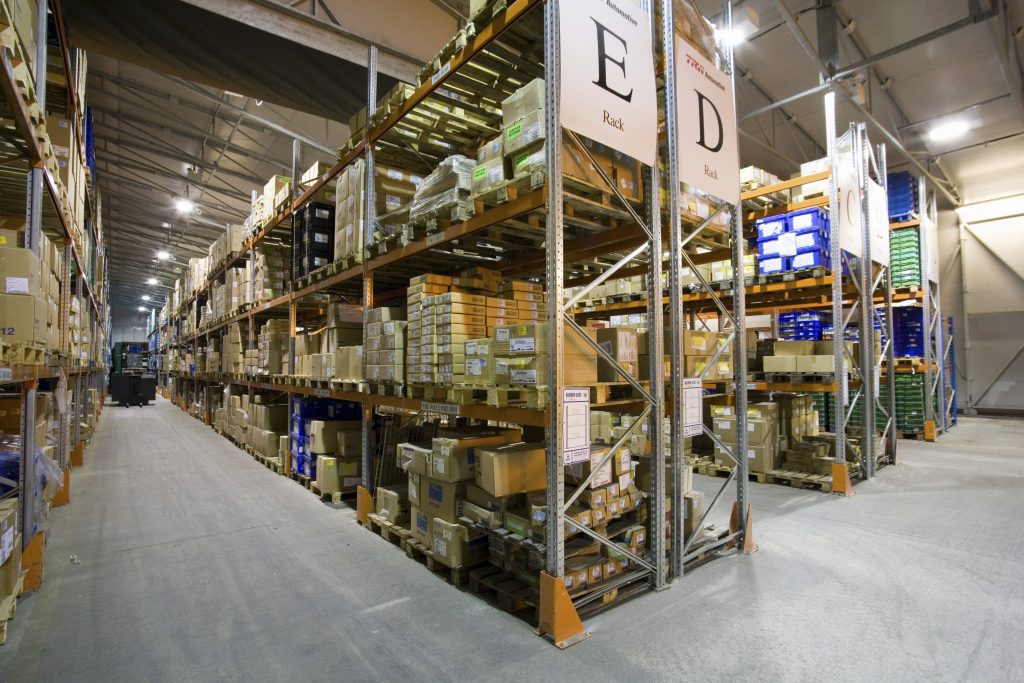
On the downside however, there are the on-going supply-chain woes. Strikes are threatened at key port locations and by fulfilment providers. There’s the war in Ukraine, Chinese lockdowns, energy prices, low-stock availability and driver shortages too. Economic predictions are currently suggesting that sales volumes will be down by as much as 13% in some sectors but not all so how can online retailers possibly plan?
We’ve read one report which says that 84% of UK businesses are considering a move to just-in-case supply chain models and that would certainly back up what we’re seeing. Demand for short-term temporary warehousing has rocketed as it can help prepare online retailers to handle a peak that may fluctuate like never before without tying them into a long-term rental agreement or forcing them to stay at a particular location. If your company generally has a single annual peak then investing in permanent warehouse space will incur a continuing cost for something that isn’t producing a return for the rest of the year.
Keeping costs low is crucial for allowing retailers to protect their own margins in the face of rising inflation while still enabling them to offer consumers competitive prices. Temporary warehousing is the most cost-effective solution for increasing space but strategically placed facilities, installed on your existing site, can also shorten the distance between the warehouse and loading areas, making you more efficient in terms of fuel consumption and energy costs too.
Temporary warehouse solutions are therefore better for your budget but also allow for flexibility. Flexibile rental periods, flexible location, flexible usage and with so much uncertainty right now, every business needs to be able to adapt!
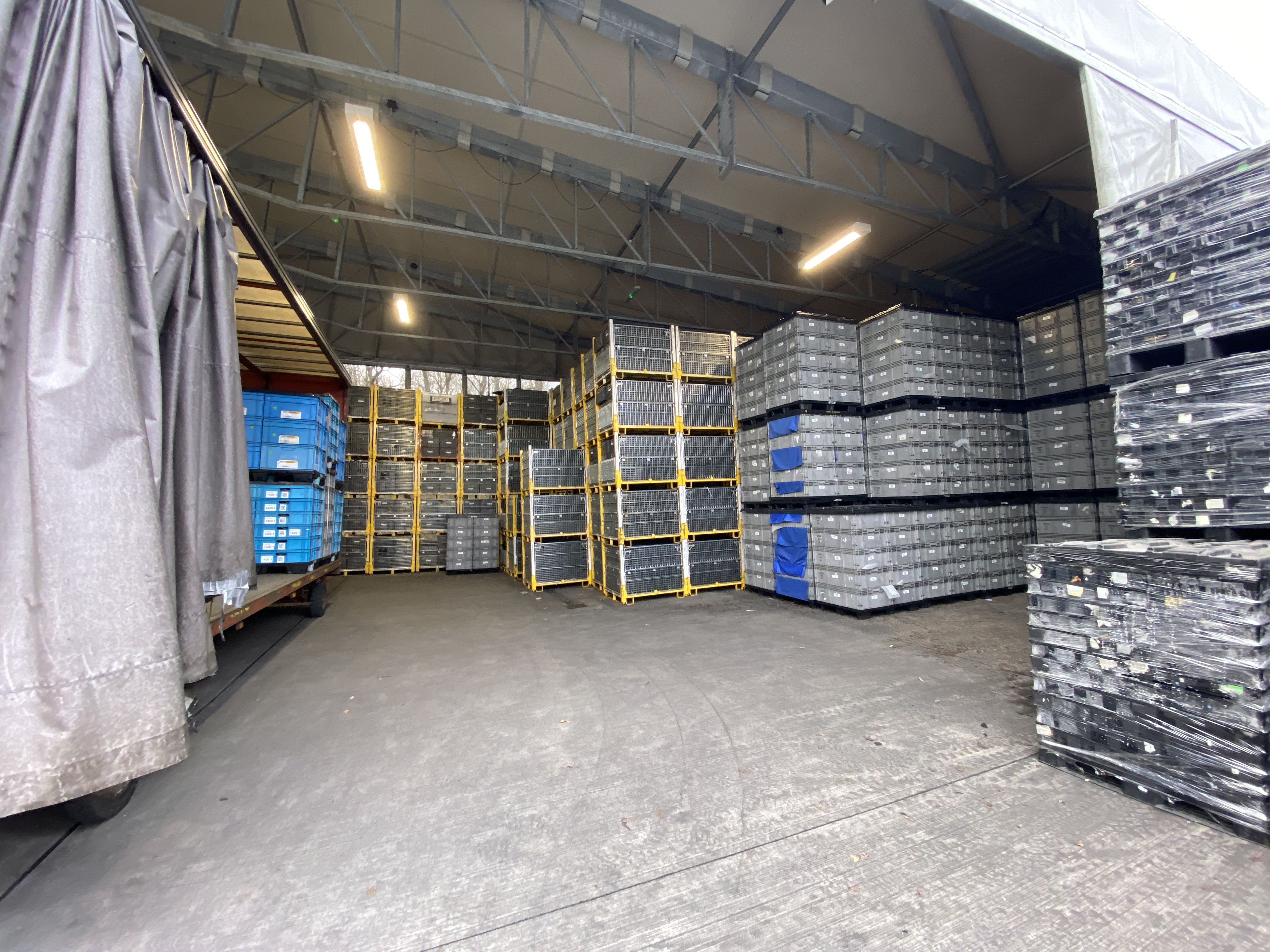
This period, from autumn half-term through to the January sales, contains most of the big spending days. Meeting this demand is essential and part of that involves finding the necessary warehouse space. A just-in-case strategy, the 2020 version of stockpiling, encourages businesses to hang on to whatever goods they can and this is increasing the demand for warehouse space even further, especially close to good distribution routes. We’re receiving lots of enquiries for smaller temporary warehouse structures located closer to the end user. Bulk storage and central distribution centres are being replaced by a more localised strategy that helps combat the rising cost of fuel, cost of delivery and shortage of drivers.
Predicting what level of stock is going to be needed and therefore how much space will be required is a challenge but a temporary structure can at least help ease the pressure, whether it is used to house excess goods, provide shelter for loading, accommodate the influx of seasonal staff who need more room for packing or is simply there, ready, just in case.