Warehouse space has become some of the most competitive property in the world. Availability is at an all-time low and sales for vacant industrial warehouses are sky-high. This shortage has been building up for a couple of years now with many wondering if the market will ever fully recover. For businesses trying their best to keep up with the rate of change, expand and continue moving forward, there is no time to hang around waiting to find out.
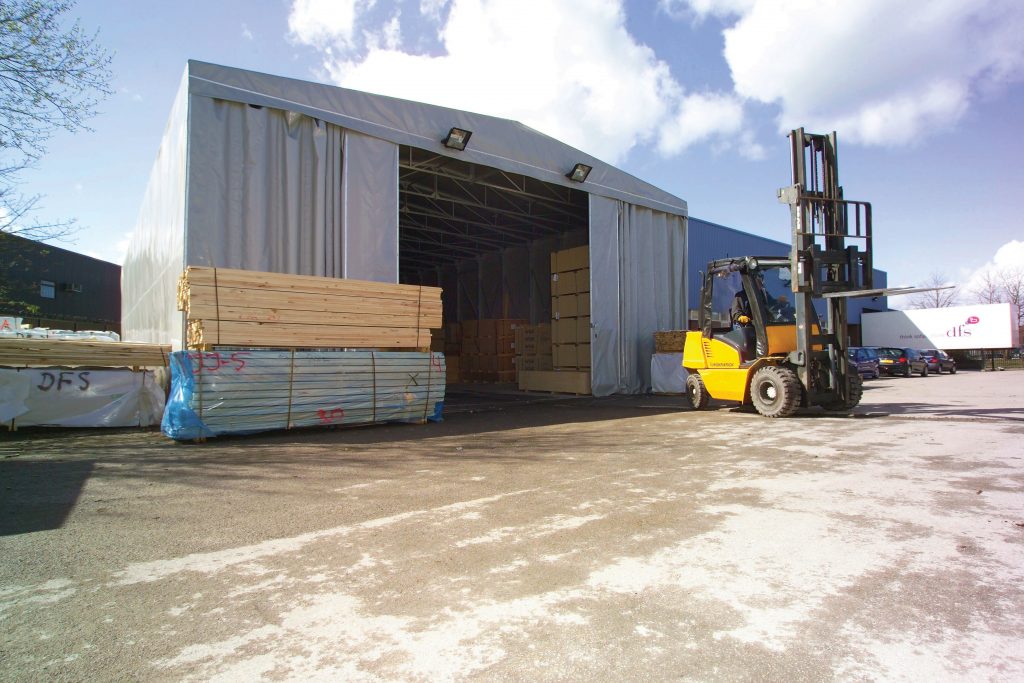
The factors that initially caused the warehouse shortage will play a major role in how soon the market bounces back but these are connected to large-scale issues at an international level and a global supply chain crisis that is causing a major bottleneck. Warehouses are full to bursting!
Online shopping was already growing year on year even before Covid came along but the pandemic put this into high-speed mode. E-commerce requires more warehouse space to begin with but the wave of demand for imported and shipped products increased the strain on warehouses even further. This consumer behaviour trend is unlikely to fade away so the influence of e-commerce is likely to continue piling pressure on the warehouse market for the foreseeable future.
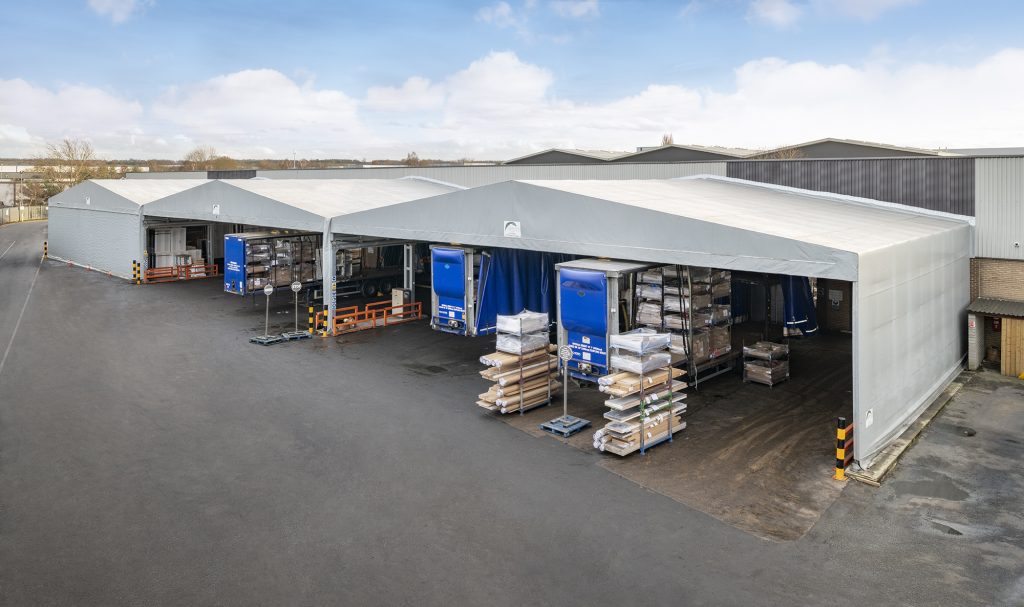
International shipping ports are operating at maximum capacity and are so congested that the stream of incoming freight for warehouses is virtually never-ending. This leaves very little time to clear out space before new shipments arrive, increasing the need for additional warehouse space.
It will take time for the global supply chain to fully recover and in that time, something else might happen to upset the apple cart. Some reports suggest that the shortage will continue until 2025 at the very earliest but most experts suggest that businesses should not look too far ahead and focus on six months at a time. They should consider adapting to a short-term strategy for growth, finding temporary solutions to the pressure on space and adopting the trend for just-in-case inventory management.
Fabric-covered warehouse structures are the answer (in our humble opinion). When CopriSystems was established over 30 years ago, we did not envisage a situation like this with temporary warehousing being one of the catalysts for business survival in a highly competitive, fast-paced and rapidly evolving industrial environment, no-one could have predicted this back then. However, we were savvy enough to know that changes would happen, whatever they may be, which is why we developed a product that was all about flexibility. Temporary fabric-covered structures were relevant then and they are relevant now because they are adaptable.
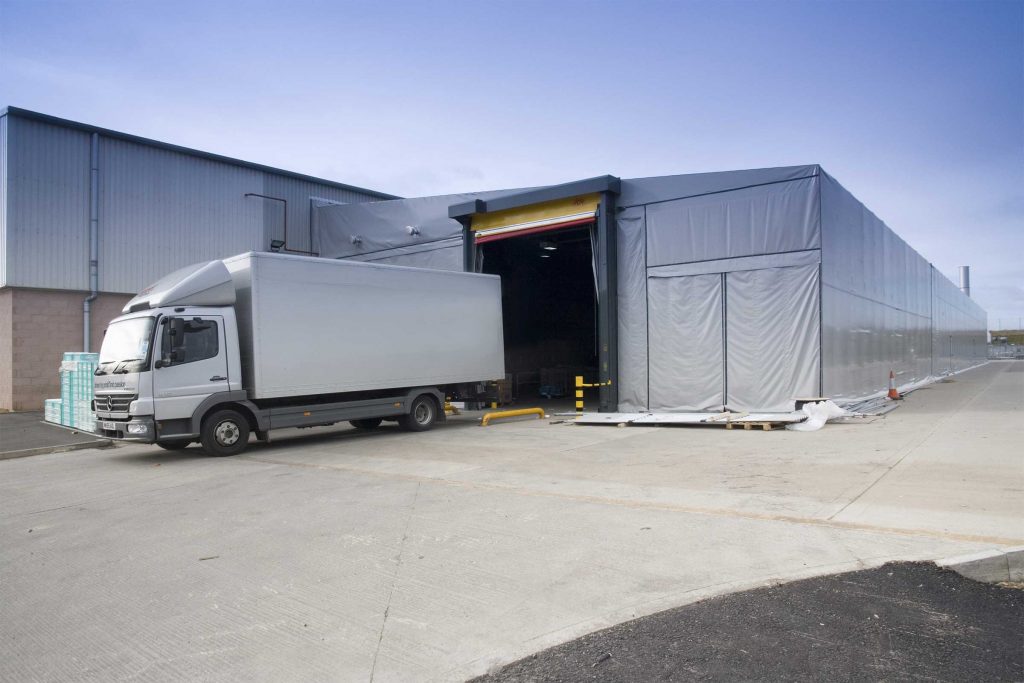
They’re also very quick to build and a major hurdle in mitigating the warehouse shortage is construction delays. The construction supply chain is under immense strain and most construction companies are understaffed today. As a result, it is taking longer than normal to build new warehouses. Fabric-covered warehouses simplify the construction process. Firstly, they are built off-site to avoid any disruption to your daily operations and secondly, they are quick to install. The whole process from design to installation takes only a matter of weeks.
They’re more affordable and fully relocatable so you can take them with you when you finally move to new premises. You may think you won’t need them then but many of our clients find them to be indispensible even if they are initially intended to make the loading process more efficient and end up being used to store machinery. Adaptability is the key to resilience.
Inevitably, the warehousing industry will adapt to today’s challenges, businesses will adapt to the market and we will continue to adapt to ensure we remain relevant.